A REINFORCED PLASTIC BIKE!
At a time when urban cycling has exploded, charged plastics are the ideal material...
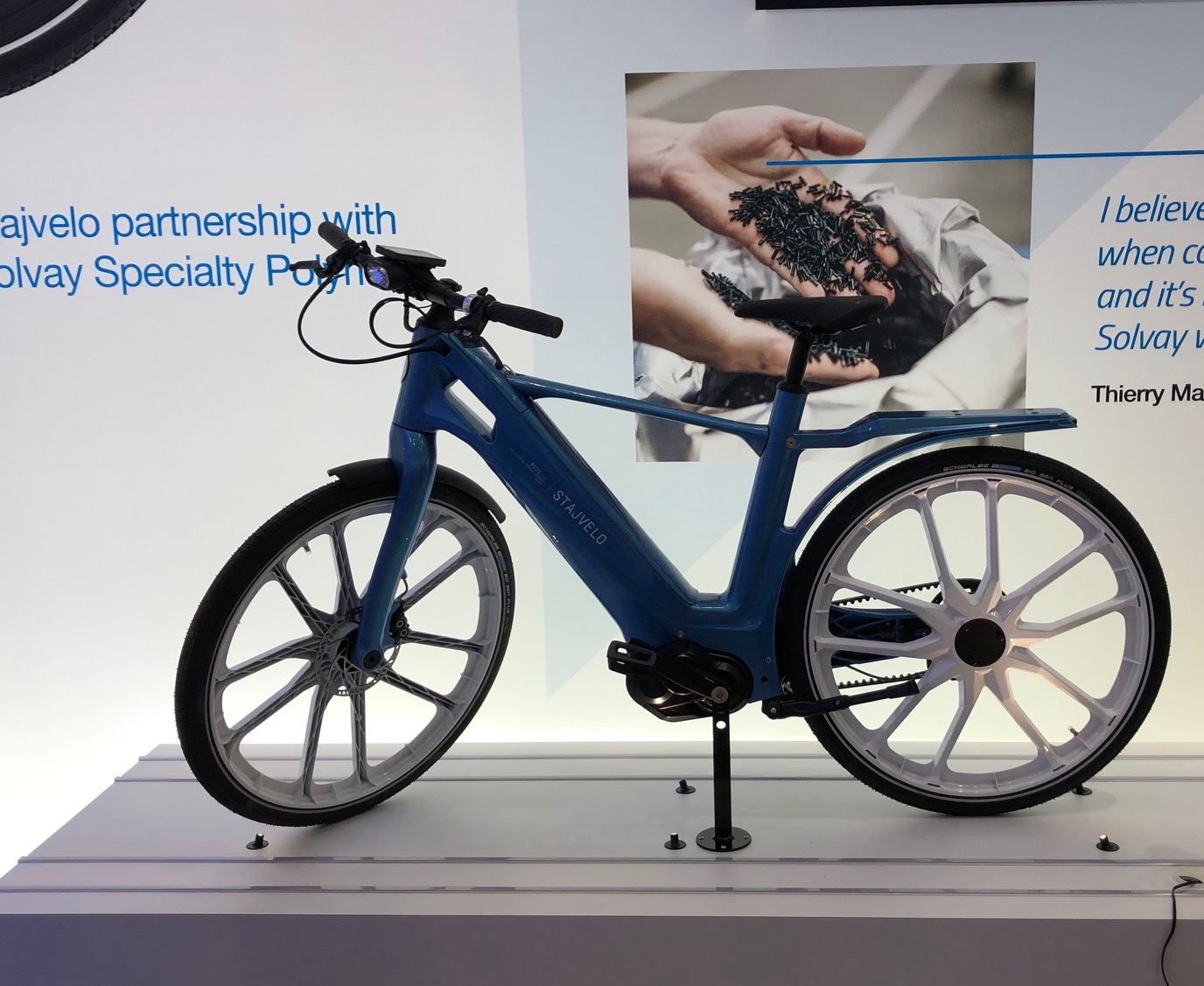
ONE STEP CLOSER TO THE URBAN MOBILITY OF THE FUTURE
At a time when urban cycling has exploded, initiatives to reinvent this means of locomotion are multiplying. Electric motors are constantly raising the technical standards of bicycle frames and wheels.
Based on the principle of form following function, plastics are the ideal materials for combining propulsion technology with attractive design.
AN AMBITIOUS PROJECT
Starting out with a blank sheet of paper to create a bicycle with a different design and approach, a Monegasque executive, a former industrialist from the automotive world and an inveterate cyclophile, approachedEDELTAMP for its expertise in injection molding of filled polymers and its ability to manage such a project.
INNOVATIVE SPECIFICATIONS
The ambition was to set new standards in sustainable bicycle manufacturing by creating new frames for a top-of-the-range electric bike, suitable for both sport and urban use.
Producing a new generation of perfectly-finished, environmentally-friendly, high-tech bicycles required the creation of frames with complex geometries and tight tolerances.
Often used in applications requiring both lightness and strength, injection molding of filled polymers was the right choice for manufacturing a frame from a single block, with no external joints or fasteners. The entireEDELTAMP team was mobilized to support the project and contribute its knowledge of thermoplastics, where the uniform distribution of aluminum powder in the polymer is essential.
FRAMES AND WHEELS 100% MADE IN FRANCE
Creating a strong, robust and durable bicycle frame in powder-filled aluminum plastic involved several key steps that were essential to achieving the desired quality objectives. In association with the design office, theEDELTAMP engineering department, in association with the design office, initially carried out structural calculations, including stress analysis, fatigue simulation and shape optimization.
OPTIMIZED MATERIALS AND PROCESSES
As part of the industrial production process, teams fromEDELTAMP teams at the Heyrieux plant have developed a unique molding process for the frame and wheels of the new top-of-the-range electric bike, which is fully injected before being finished with epoxy paint.
The logistics and storage of raw materials and components were managed by EDELTAMP in order to reduce supply distances before the bike could be fully assembled and assembled in the customer's workshop in Monaco.
HIGH-TECH DESIGN
Electric-assist bikes come in all shapes and sizes, with frames usually made of steel or aluminum.
Opening the doors to innovation to achieve optimum performance with great comfort even over long distances, the design of the project industrially produced by EDELTAMP has been designed for high stability and rigidity, precise handling, and optimum transmission of the energy of electric assistance and pedaling.
Thanks to a modular design, the wheel structure can be used for both front and rear wheels. They are monobloc, broached according to tubeless standards, and can be disassembled without the need for special tools. The choice of injecting the wheels with a plastic filled with aluminium powder has enabled them to absorb shocks and vibrations, thus reducing muscle fatigue.
Available in several versions to suit urban use, the electric bike's design features an open frame for easy straddling. Depending on the options chosen, the modular capacity of the thermoplastic components enables the adaptation of a horizontal stem for a sporty look and increased rigidity.
Undeniably elegant, the aluminum-powder-filled thermoplastic monocoque frame, finished with a gloss epoxy paint coating by EDELTAMPThe frame integrates absolutely everything: the central motor, transmission, cables and battery. Nothing is visible from the outside, everything is just a suggestion.
EDELTAMP AND MOBILITY
Producing small, medium and large series, EDELTAMP continues to deploy its excellence in both industrial and consumer mobility.
For over 30 years, EDELTAMP has become a benchmark in the design and manufacture of thermoplastic injection molds, integrating the entire production chain at your service.
Every year, our expertise as a tool and die maker is called upon by international industrial customers for the production of plastic parts in a wide range of sectors, including agriculture, the capital goods industry, leisure and gardening, mobility, construction, wellness, as well as handling and lifting.
The operational knowledge and excellence of our workers in the manufacture of high-precision steel molds guarantee you the highest quality in the industrial manufacture of plastic parts, from the molding of the most innovative prototypes to the overmolding of the most complex technical parts.
Other articles in this category
Keep up to date with EDELTAMP and how we're shaping the future of the plastics industry .