THE REASONED APPROACH TO THERMOPLASTIC ELASTOMER INJECTION MOULDING
Produce the best technical product, taking into account product life-cycle analysis...
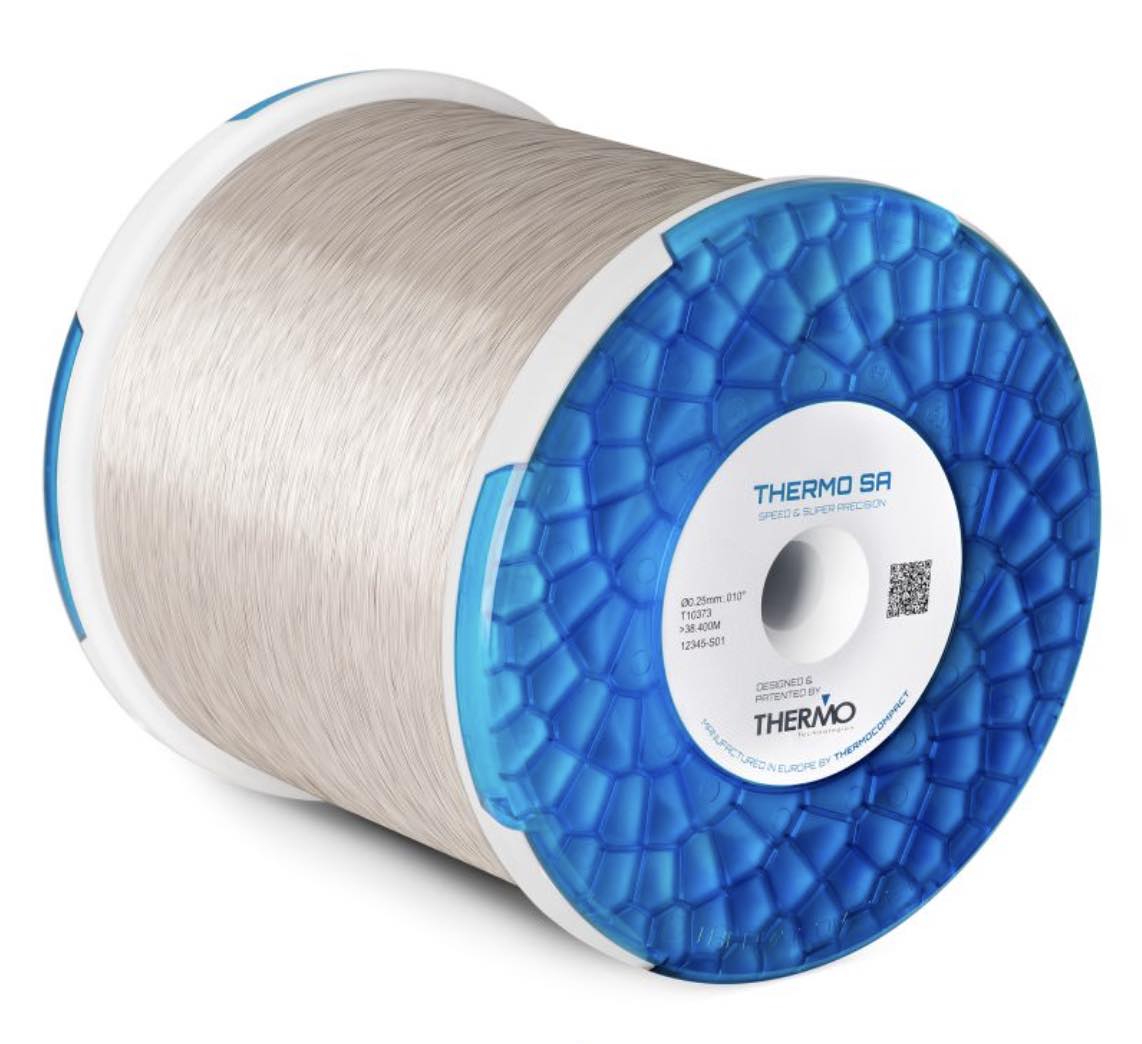
Since its creation, THERMOCOMPACT has excelled in two fields: surface coating with precious metals and high-tech specialty wires.
THERMOCOMPACT is the world leader in electrical discharge machining (EDM) wires, manufacturing innovative EDM wires that enable high-tech industries, as well as general and precision engineering sectors such as automotive, aeronautics, space, connectors and precision mechanics, to achieve major productivity gains by optimizing their machining speed and cutting precision.
In order to be able to supply its customers with several thousand meters per year of these top-of-the-range wires in perfect winding and storage conditions for its entire range of EDM wires, THERMOCOMPACT called on EDELTAMP to produce its spools.
The spool design consists of a cylindrical core and two white flanges at the ends. A transparent trim in primary or secondary colors covers the sides, enhancing product recognition according to the technical specificity of the EDM wire.
Mould development, thermoplastic injection, mechanical assembly of components and logistics management are handled by theEDELTAMP teams at our Heyrieux plant.
For sustainable and responsible production
Based on fundamental values aimed at manufacturing the best support for the best technical product, the specifications for its entire production cycle consisted in taking into account, and reducing, the integration of environmental aspects in the industrialization and production phases alongside the usual criteria.
The life-cycle analysis of coils has been revisited in terms of sustainability and environmental footprint. Coils produced by EDELTAMP guarantee total recyclability of the raw material, without the need for prior disassembly of their components.
The performance of industrial know-how
EDELTAMP has become a benchmark in the manufacture of injection-molded plastic parts on presses ranging from 60 to 1,800 tons, with production volumes ranging from small to large runs.
Every year, our expertise in thermoplastic elastomer injection molding is called on by European and international industrial customers for the production of plastic parts in a wide range of sectors, including agriculture, industrial and consumer capital goods, leisure and gardening, mobility, construction, wellness, and handling and lifting.
As a reminderEDELTAMP confirms its development plan for 2024 and continues to expand at its Heyrieux site with the addition of a building for a total of 5,800 m². Thanks to its new layout and the addition of new machinery and control equipment, the company can rely on its team and design office to meet the challenges of the future on a European scale.
Other articles in this category
Keep up to date with EDELTAMP and how we're shaping the future of the plastics industry .